What
information is needed by a brush manufacturer to make a brush?
Generally it is a matter of
adequately describing the existing brushes if they are performing well,
provided no other changes are required.
Alternatively a sample can
be supplied, though if it is worn then you will have to give the length
required for the new brushes. If this is not known then look at a worn
brush in the brush holder and pull the brush away from the commutator as
far as possible, ensuring the spring remains comfortably positioned on
top of the brush.
Take a measurement from the
top of the brush to the commutator for the new maximum length.
To assist in providing all
relevant details, data sheets which indicate the required information
are available from Morgan Industrial Carbon. These forms will generally
supply sufficient information to manufacture the most common brushes.
The width and thickness
dimensions are the most critical pieces of information.
IEC and AS standards have
defined certain standards for nominal dimensions and appropriate
tolerances. It is important to note that many problems have been
introduced by, identifying a brush as 16mm x 32mm when the holder was in
fact 5/8" x 1 1/4".
it is very important to
determine if the brush is metric or imperial measurements. If there is
any doubt the country of machine manufacture will usually give an
indication.
American motors and older
English motors are usually imperial while European motors have generally
been metric.
Most European suppliers
manufacture brush holders with built in clearance to suit current IEC
standards, which specify a clearance above the nominal brush size. Other
holders may have no clearance or different clearances and brushes should
be made to suit them.
Caliper holders need only to
clamp or bolt firmly the carbon block and therefore require no special
clearances.
The grade is very important.
If the existing grade is not known then the nameplate information, along
with any operating conditions such as running current, needs to be
supplied to the brush manufacturer.
Back to Top
Why do
brushes wear sometimes differently in the same machine?
On DC slip rings of
alternators and synchronous machines, because of the polarity of the
current conduction, the build up of the patina and the wear on the slip
ring and brushes can often be different. It can be balance out by
periodically reversing the connections to the rings. This does not
become a problem in DC machines because each brush track will
havepositive and negative brushes on the same track.
It is not unusual for
brushes to wear slightly unevenly in a DC machine though in an ideal
situation they would all be the same.
Differences in individual
brush tracks on a commutator will affect all brushes on that track. This
has to do with the condition of the patina or film and also the shape
and surface condition of the commutator in that particular position.
Grooves and flats or
irregularities, can be the reason for increased wear on a row of
brushes. Incorrect brush holder positioning can also be a cause.
If brushes on the same track
have differing wear, brush holder condition, in particular spring force
can be a contributing factor. Uneven force will have a significant
effect on how brushes share the load and wear electrically.
The condition of pivot
points for the arms which can become seized or tight can also affect
spring force and the condition of the inside faces of the brush holder.
Back to Top
Why do
replacement brushes sometimes appear to wear more than the original set?
The more common reason for
increased wear is the deterioration of the commutator surface which
occurs over time, so in fact even if genuine original brushes were
fitted they too would not last as long as the original set or sets which
operated on a new or near new commutator. This is a very common
occurrence with high speed series motors, appliance motors and
fractional horsepower DC motors which do require commutator remachining
from time to time.
Often the grade selection by
the machine manufacturer has been the result of testing over a long
period. The brush grade may not be marked on the brush due to lack of
space on smaller brushes, or the machine manufacturer may reveal only a
reference number to try and capture the spare parts aftermarket.
This can mean that
alternative replacement brush grades are selected from general
experience with similar motors and their performance may not be exactly
the same as the original. The usual high prices of original spares may
still make alternatives more economical, even if they are not lasting
quite as long or require trials of more than one grade to achieve
acceptable performance.
Back to Top
Why do some
commutators show regular light and dark patterns on the segments?
This condition usually
relates to the original machine design.
Due to the fact there
are more commutator segments than coil slots in the armature, some
individual coils in the group fitted in a particular armature slot will
be less favourably positioned in relation to the true neutral position.
Also the number and
positioning of equalising connections may have an influence on some bars
and not others. Generally this is not detrimental to the machine and can
be ignored.
If burning or detrimental
effects are evident on some bars then the grade will need to be changed
to improve the commutation.
The possibility of the
introduction of circumferential stagger may also be considered if the
problem still exists. This should be done in conjunction with with the
machine supplier or brush manufacturer.
Back to Top
How should
a spare motor, fitted with brushes, be stored?
If a motor is to be stored
for a long period of time it is advisable to lift the brushes off the
commutator surface. This is to avoid the possibility of marking the
commutator due to galvanic action under the brush face. While suitable
pads can be placed between the brush and commutator it is best to have
nothing in contact with the commutator so its surface condition is
consistent over the entire area.
Releasing the spring
pressure and pulling the brush back in the holder is preferable.
Ensure that the terminal box
is fitted with a warning to refit the brushes correctly prior to placing
the machine back into service.
Back to Top
How do you
select the "right" grade?
While published technical
data and application guides can be of great assistance, an important
part of the duties of the application specialist is to study reports on
brush operation in service. Although laboratory tests can be a guide in
assessing the relative characteristics of different grades, the ultimate
test as to suitability must be made on the machine itself.
Due to this fact, progress
in the development of new and improved grades is largely dependant on
the co-operation of users in allowing access to their machines for
observation.
Much of the accumulated
knowledge on brush design, construction and operation is the result of
the correlation of reports on the behaviour of brushes in service
received from customers and from engineering representatives resident in
all parts of the world.
Generally speaking brush
specialists are best qualified and usually available to make the grade
selection for you, however it may not be possible to gain optimum
performance on the first selection. Some patience and time can be
required to ascertain the best grade for a particular application.
Back to Top
Morgan
Industrial Carbon
Products
| Literature | Contact Us |
About Us | News | Home
Locations and Addresses
Sydney
Tel : 0061 2 9772 5600 |
Brisbane
Tel : 0061 7 5433 7100 |
Melbourne
Tel : 0061 3 9551 2377 |
Perth
Tel : 08 9451 9088 |
Auckland
Tel : 0011 64 9 836 9220 |
Singapore
Tel: +65 6296 0929 |
Malaysia
Tel: (60) 3 - 5569 3990 |
Morgan Carbon
A Division of Morgan Crucible
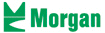
sales@morgancarbon.com.au