Commutator
condition chart
COMMUTATOR
SURFACE CONDITIONS
Satisfactory
Conditions
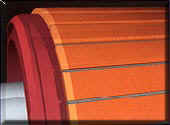 |
Light
Film - over the entire commutator surface is one
of the many normal conditions often seen on a well
functioning machine. Film tone is dependent on the
brush grade and current density. |
|
|
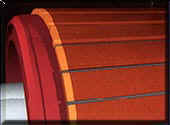 |
Dark
Film - if uniform over the entire commutator
surface is acceptable. This condition can be the
result of a high filming brush grade, higher current
densities or the presence of chemical vapour
contamination. |
|
|
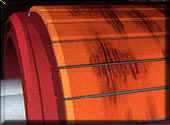 |
Blotchy
Film - this non uniform filming condition is the
most common appearance. The accumulated tolerances in
the machine such as commutator roundness brush contact
pressure, unequal magnetic fields and chemical vapours
all contribute to this type of film development. |
|
|
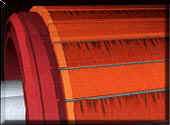 |
Slot
bar Filming - repeating light end dark filming
patterns related to the number of armature coils per
slot. This pattern is dependent on the machine design
and usually not a function of the brush grade. |
Conditions
of Concern
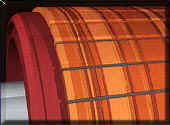 |
Streaking
- of only the film is not detrimental to the
commutator. Brush and commutator life are not at risk
in this condition. If metal transfer develops, this
condition will progress into threading. This type of
filming can be dependent on current density or brush
grade. |
|
|
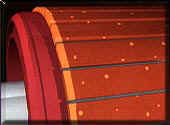 |
Bright
Spots - a freckled appearance of the film usually
caused by machines that are subjected to frequent
overload cycles. If the bright spots disturb only the
film, a machine can operate for long periods of time
with this condition. If severe metal transfer begins,
the bright spots could progress to dangerous bar
burning or film stripping. |
Unsatisfactory
Conditions
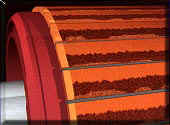 |
Bar
Burning - is the erosion of the trailing edge of
the commutator bar. Failed machine components,
misadjusted electrical symmetry of the machine or a
poor commutating brush can result in bar burning. If
not corrected, this condition can cause severe
commutator damage or a flashover. |
|
|
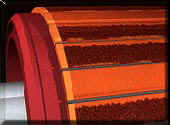 |
Slot
Bar Burning - results in commutator erosion of
every second, third, or fourth bar depending on the
winding design of the armature. Improper brush
material, brush design or electrical adjustment of the
machine can cause this condition. This condition
severely damages the commutator and reduces brush
life. |
|
|
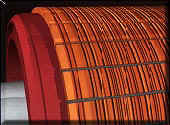 |
Threading
- is machining of the commutator by copper
particles in the brush face. The excessive copper
transfer occurs due to low spring pressure, light
loading or contamination. These particles are trapped
in the porous carbon brush and work harden, creating a
tool that machines or Gaul's the commutator surface.
The machine can operate for long periods of time with
this condition, but reduced commutator and brush life
will be experienced. |
|
|
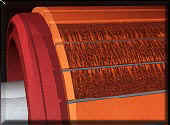 |
Pitch
bar Burning - results in commutator bars being
eroded in a pattern related to 1 /2 the number of
brush arms, progressing into a pattern equal to the
number of brush arms. This condition is caused by a
cyclic mechanical or electrical disturbance such as,
on unbalanced armature, misaligned shafts, bent shaft,
bad bearings, weak foundation, foiled equalizers or a
poor riser connection. If not corrected this condition
will result in a flashover. |
|
|
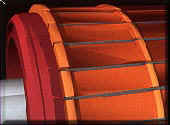 |
Grooving
- is the uniform circumferential wear, the width
of the brush that is exhibited on the commutator.
Excessive abrasive dusts in the atmosphere or on
abrasive brush can cause this condition. Extreme light
spring pressure (below 1 .5 psi) can also cause this
condition. Proper brush applications and filtering the
air on force ventilated motors can reduce the
commutator wear, Some people call this
"Ridging" because of the resulting ridges on
each side of the groove. |
|
|
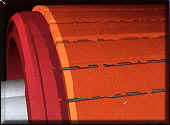 |
Copper
Drag - occurs when high energy transfers copper in
a molten state. These particles become coated by
contaminants from the surrounding environment or the
brush treatment and do not oxidize properly to form
the film on the commutator surface. These particles
accumulate at the edge of the bar, eventually shorting
across the insulating mica. This condition needs to be
addressed immediately when discovered or serious
damage may occur. Chamfering the commutator bar edges
is necessary to stop the progression of this
condition. |
|