Bearing components
Carbon and graphite bearings
Applications
Carbon / graphite and carbon filled PTFE bearings are used where oil or grease lubricated bearings can only be used with difficulty, if at all.
Carbon / graphite bearings can run dry, using the natural lubricating properties of the carbon/ graphite material, or they can be fully immersed in liquids such as water acids, alkaline solutions and solvents. It is preferable that the bearings are either fully immersed in the liquids or run completely dry.
Principle Fields of Use are:
- Where contamination is undesirable as in textile and food machinery i.e. by avoiding the use of oil or grease. PTFE with various fillers can successfully be used in these applications.
- In oven, furnace and boiler equipment where working temperatures are too high for the use of conventional lubricants.
- Where the bearings are immersed in liquids such as hot and cold water, sea water, acidic and alkaline solutions or in solvents such as petrol and benzines. Example, submersible and centrifugal pumps.
- Where other bearing material cannot be installed owing to the danger of corrosion.
Properties
of Carbon Bearing Materials
- Good frictional qualities
- High thermal resistance
- High corrosion resistance
- Very good chemical resistance
- Low thermal expansion
- Outstanding resistance to thermal shock
- Good form stability even at high temperatures
- Good thermal conductivity
As carbons can be impregnated with various materials such as resin, antimony, lead bronze and white metal to increase bearing life according to the application, Morgan Industrial Carbon should be contacted when designing these bearings to ensure correct grades are to be used. |
|
Typical information needed to advise material grade would be:
- Is the bearing to be used in a dry or wet running environment?
- Product in which the bearing is to be used (type of liquid if wet running).
- Bearing operating temperatures.
- Type of machine.
- Radial, thrust or sliding bearing.
- Continuous or intermittent duty.
- RPM______or m/sec surface speed______
- Bearing load.
|
Bearing Design
In principle, design should follow the recommendations given below:
- bearings for dry running should have a smooth bore.
- no oil, grease or abrasive dust should contaminate the rubbing surfaces of a dry running bearing.
- when bearings are running wet, bores should have spiral grooves or axial grooves according to the application
WRONG |
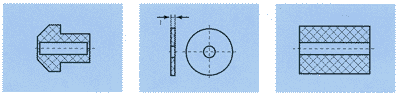 |
RIGHT |
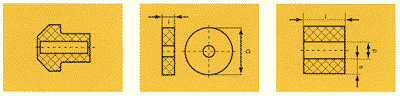 |
Avoid sharp steps in the bore and on the inside. Break sharp edges |
Dimension I < 0.1 D, if possible not below 3mm |
< 2 D
s = 0.15 ...0.2 . d
smin = 3mm |
|
WRONG |
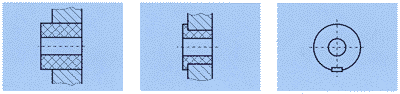 |
RIGHT |
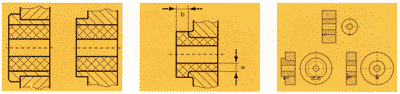 |
Cylindrical bearings should be fully supported by the housing or by a special metal bush. |
Flange thickness should be at least equal to wall thickness. A transitional angle should be radiused. Housing thrust face for flange to be machined.
b > 5 . |
Any arrangement to prevent rotation such as a check plate or plain pin, should be in an unloaded area not in the bore.
Any keyway should be axial and milled out carefully to avoid breakage. |
|